BCCK designed NiTech® as a nitrogen rejection technology that eliminates cryogenic rotating equipment and allows for a wide variation of inlet nitrogen concentrations. Cryogenic rotating equipment is consistently responsible for facility downtime and excessive operating expense due to its high power consumption and maintenance requirements.
Furthermore, NiTech® features a simple process design requiring minimal operator attention comprising only five major components. This reduces capital costs (CAPEX) and delivery time when compared to conventional technology. The success of the flagship NiTech® NRU in Oregon prompted the installation of 28 additional NiTech® facilities in the domestic United States. Although each unit is centered on the core NiTech® design, each facility has unique challenges due to differing gas compositions, flowrates and operating conditions.
During the 25-year history of NiTech®, there have been three major revisions to the process design. Style III represents a new design that allows greater flexibility with respect to compositional changes or flow capacity changes than ever before. With better efficiencies on residue gas compression, NiTech® Style III is a highly competitive addition to the marketplace. It can be modified to produce LNG and can be customized to extract incoming helium and NGL’s from the inlet gas stream. In addition, where methane emissions are critical, the base NiTech™ III unit can be configured with a vent stream purifier to reduce the vented methane to extremely low levels. With the purifier installed, the vented stream would contain between 0.1 and 0.2 percent methane.
NiTech® technology is not constrained by low mole % nitrogen gas streams and does not require a nitrogen recycle stream costing additional capital and operating expenses (OPEX). NiTech® can process inlet gas to less than 1.0 mole %, allowing BCCK to slipstream and reduce a customer’s CAPEX and OPEX requirements. The ability to handle higher mole % nitrogen in gas is important in meeting downstream pipeline specification and the fact that the NiTech® process emits no non-methane volatile organic compounds (VOCs) makes it an environmentally friendly solution, achieving 99% or greater hydrocarbon recovery.
As a result of BCCK’s proven successful track record with the technology, in 2018, Navitas Midstream Midland Basin, LLC, chose to incorporate a second NiTech® Style III in the construction of a nitrogen rejection unit (NRU) in West Texas. The unit is designed to process natural gas with concentrated nitrogen on the residue of a new cryo plant.
+To find out more about the NiTech® process, benefits and see a selection of NRU facility photos.
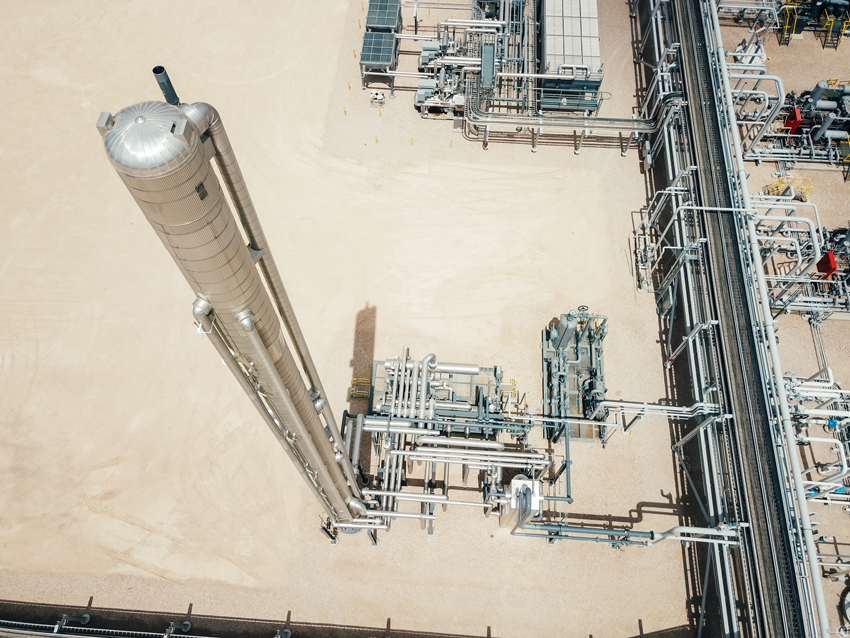
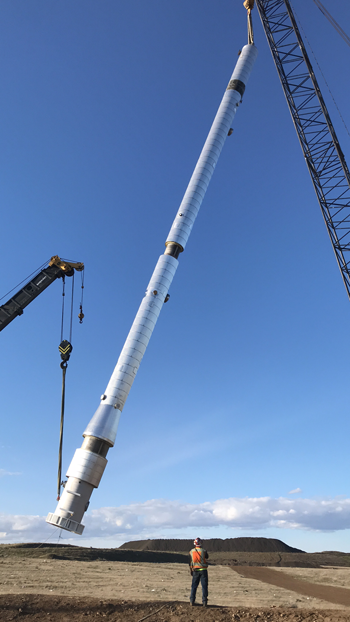