Understanding NiTech® NRU Styles and Applications
NiTech® Nitrogen Rejection Units (NRUs) are engineered to effectively separate nitrogen from hydrocarbons across diverse applications. These systems are widely used in the oil and gas industry, biogas processing and LNG facilities. With three primary configurations—single column, dual column and ULM (Ultra Low Methane) models—NiTech® NRUs offer tailored solutions for varying operational needs. This article explores the unique features, technical differences and applications of each NiTech® NRU style to help you determine the best fit for your project.
The Core Process Behind NiTech® NRUs
All NiTech® NRUs incorporate cryogenic distillation, a highly efficient method for separating nitrogen from hydrocarbons. This process relies on auto-refrigeration, where feed gas is cooled to cryogenic temperatures using various internal process streams, eliminating the need for auxiliary coolant systems. Using heat integration, NiTech® NRUs reduce operational costs and maintain system efficiency.
It is important to note that NRUs do not eliminate all nitrogen from the gas stream. Depending on the application, these systems aim to reduce nitrogen content while maintaining acceptable vent purity levels, adding operational precision and efficiency.
NiTech® NRU Styles
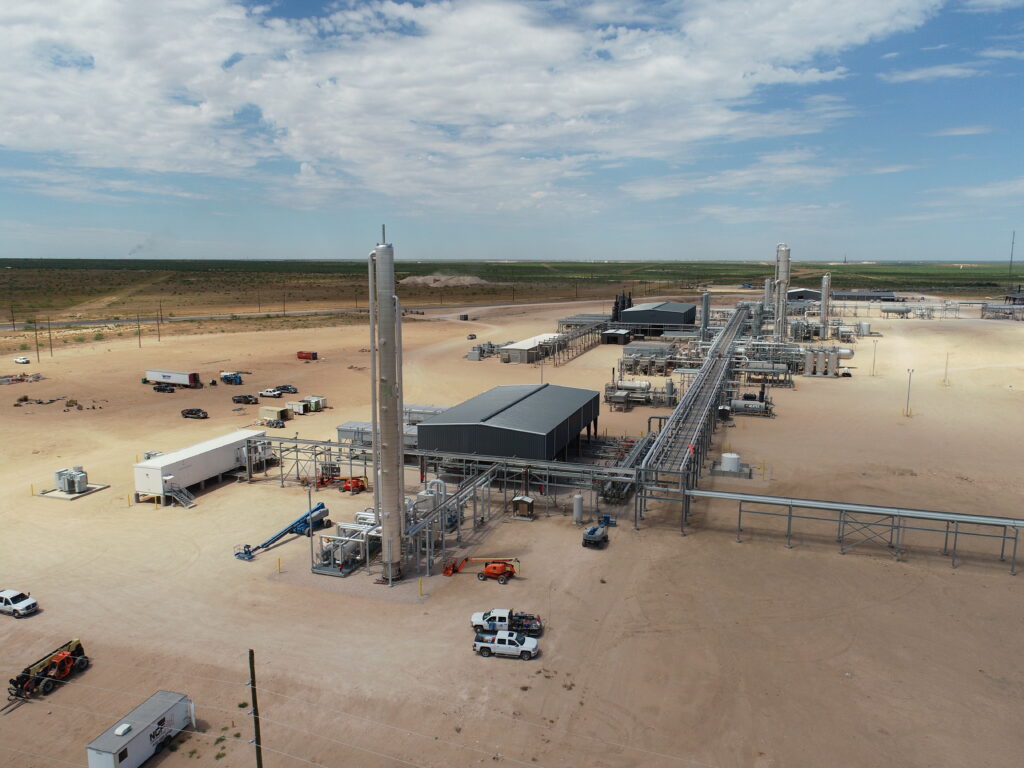
Single Column NRUs
Key Features:
- Compact design with lower upfront capital investment.
- Operates efficiently for low flow rates and lower nitrogen compositions.
- Commonly used for smaller-scale applications, such as biogas from landfills or coalbed methane processing.
Applications:
Single-column systems are ideal for small-scale projects that prioritize simplicity and lower cost of entry. Organizations in need of moderate nitrogen removal typically choose this style.
Advantages:
- Simple design and easy maintenance.
- A cost-effective option for operators with less stringent vent purity requirements.
Limitations:
- Limited capacity to handle high flow rates or nitrogen concentrations.
- May not meet strict environmental regulations for methane slip in specific applications.
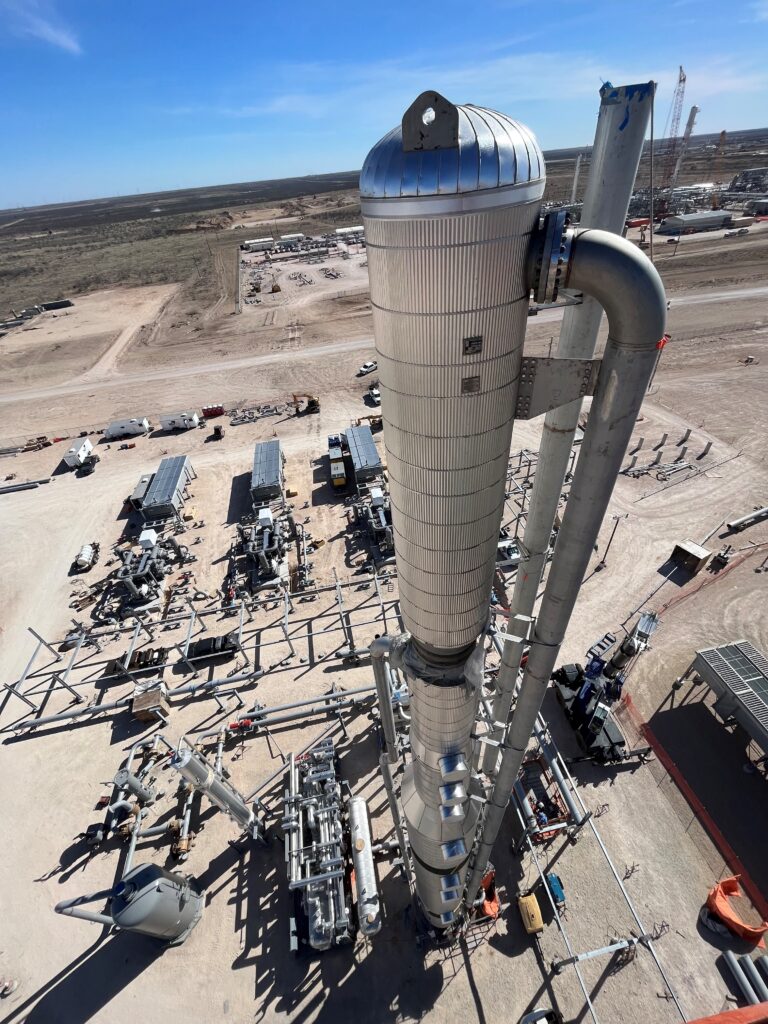
Dual Column NRUs
Key Features:
- Two columns for enhanced separation performance.
- Capable of processing higher nitrogen compositions and higher inlet flow rates.
- Mixes efficiency and scalability for most gas processing needs.
Applications:
Dual-column systems are versatile and well-suited to gas plants with moderate flow rates and intermediate nitrogen levels. They balance cost, efficiency and performance.
Advantages:
- Higher throughput compared to single-column systems.
- Meets a broader range of nitrogen composition requirements.
Technical Difference:
Some dual-column NRUs on the market treat all gas streams in both columns, which results in higher equipment and energy costs. NiTech®‘s approach focuses on treating the bulk gas in the first column, with only a smaller stream processed in the second column. This design lowers capital costs and reduces operational complexity without compromising performance.
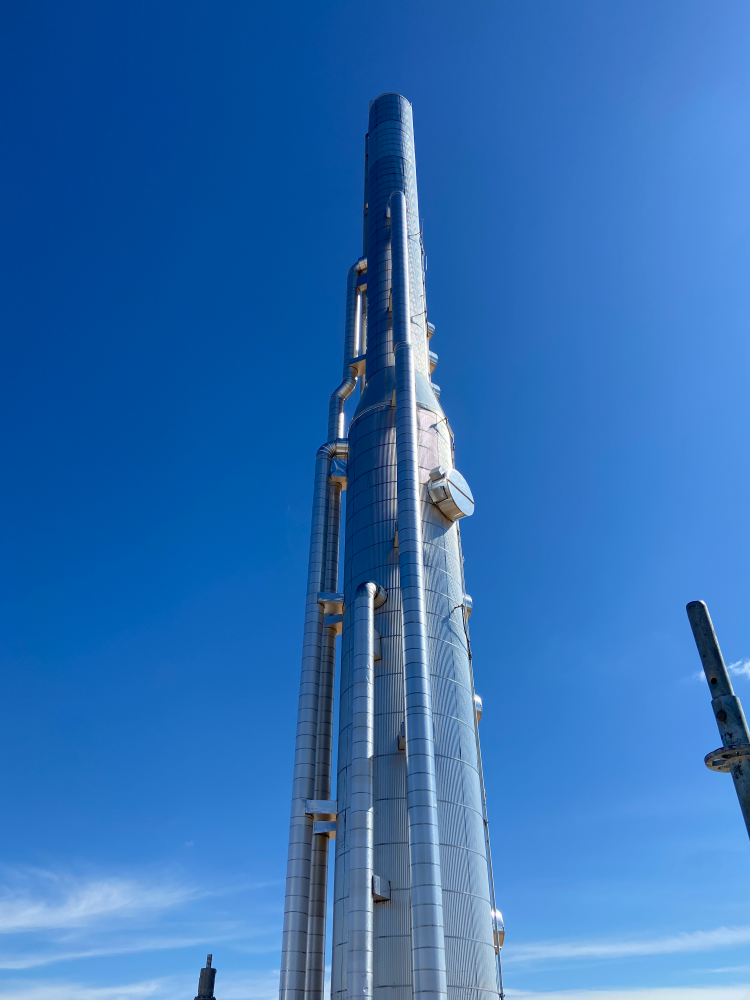
ULM (Ultra Low Methane) NRUs
Key Features:
- Advanced design tailored for stringent vent purity requirements.
- Reduces methane loss to fugitive emission levels.
Applications:
ULM systems are commonly used in LNG export facilities and other operations requiring strict compliance with government and federal environmental regulations. These applications involve high flow rates, meaning any fraction of methane recovery lost is several tons per year, making ULM systems essential for maximizing methane recovery and reducing emissions.
Advantages:
- Best-in-class methane recovery, minimizing greenhouse gas emissions.
- Meets or exceeds the strictest regulatory standards.
Limitations:
Higher initial capital costs due to the system’s complexity and advanced features.
Choosing the Right NiTech® NRU Style
When selecting the appropriate NRU style, there are several critical factors to consider:
Inlet Flow Rate
The magnitude of gas flow significantly influences NRU design.
- Low flow rates (<10 MMSCFD) align better with single-column systems.
- Moderate flow rates (10-200 MMSCFD) perform optimally in dual-column systems depending on nitrogen composition.
- High flow rates (>200 MMSCFD) are typically suited for ULM systems, especially in LNG facilities.
Nitrogen Composition
Nitrogen content in the feed gas determines the required separation capacity:
- For moderate compositions (<10%), single or dual-column systems are cost-effective options.
- Higher compositions (10-15%) often necessitate dual-column systems with enhanced design considerations.
- When vent purity is critical (e.g., LNG export standards), ULM systems are the preferred solution.
Regulatory Compliance
If compliance with federal or state regulations—such as minimizing methane emissions—is a key concern, choosing a ULM system ensures the highest standards. If there is any concern about future regulations for methane, then it is recommended that the NRU be “future-proofed.” This consists of adding process connections and implementing equipment modifications to accommodate a future retrofit to the ULM-style NRU.
Operational Considerations
Factors like startup/downstream processes, onsite power availability and system maintenance also play a role. BCCK’s NiTech® NRUs are designed to balance capital expenditure (CAPEX) and operational expenditure (OPEX), offering customized solutions tailored to client goals.
Understanding Auto-Refrigeration in NiTech® NRUs
NiTech® NRUs rely on auto-refrigeration. By eliminating the need for auxiliary refrigeration loops in most cases, NiTech® NRUs reduce capital costs and system complexity. The auto-refrigeration design effectively pre-cools gases for the cryogenic distillation process, leading to unmatched efficiency in separation.
However, operators must account for the time required to cool down the system during commissioning or after extended shutdowns. Depending on initial conditions, NiTech® NRUs require 1-2 days on average to achieve full operational capacity.
BCCK’s Differentiator: Experience and Expertise
Over the years, BCCK has played a pivotal role in designing and commissioning NRUs for various industries worldwide. With over 41 operational units and handling billions of cubic feet of gas daily, BCCK has built a reputation for delivering accurate, efficient and reliable solutions.
Unlike competitors, our expertise is built on operating experience, not simulation models alone. We incorporate actual facility data and implement lessons learned after every successful project for all future designs to ensure long-term system reliability and ease of operations. Providing clients with peace of mind that their systems will operate optimally in real-world conditions.
Selecting the proper NiTech® NRU configuration is vital to achieving operational efficiency, maintaining compliance and minimizing costs. With its suite of single-column, dual-column and ULM models, BCCK offers tailored solutions for various applications.
Our experience and attention to detail ensure that your system operates as expected, delivering value from day one.
Are you curious to learn more? Contact a BCCK engineer today to find out how we can support your project with the right NiTech® NRU solution for your needs.