Trusted Solutions for Superior Natural Gas Processing
Nitrogen rejection has been a cornerstone of BCCK’s business since the late 1980s. Recognizing the need for an efficient and cost-effective nitrogen rejection process for natural gas streams, founder Clark Butts developed and patented the NiTech® process. Today, BCCK’s NiTech NRU technology serves natural gas streams ranging from 5 MMSCFD to over 500 MMSCFD, allowing operators to recover reserves that were previously uneconomical due to nitrogen, CO2, helium, oxygen, or other contaminants. The NiTech process is designed with a focus on minimizing methane emissions, providing environmentally conscious solutions for natural gas processing facilities.
The NiTech NRU offers an efficient design with reduced horsepower requirements, high methane recovery, and a lower-cost, more reliable system. Whether using a single or dual tower configuration, NiTech has become the go-to solution for nitrogen rejection in both high and low N2 inlet gas streams.
BCCK has also introduced NiTech® ULM, a patent-pending enhancement designed to achieve ultra-low methane vent levels, setting a new standard in emissions control. This innovative solution not only cuts methane losses but also helps operators comply with Environmental Protection Agency (EPA) regulations while reducing environmental impact.
>> Learn more about our Nitrogen Rejection experience.
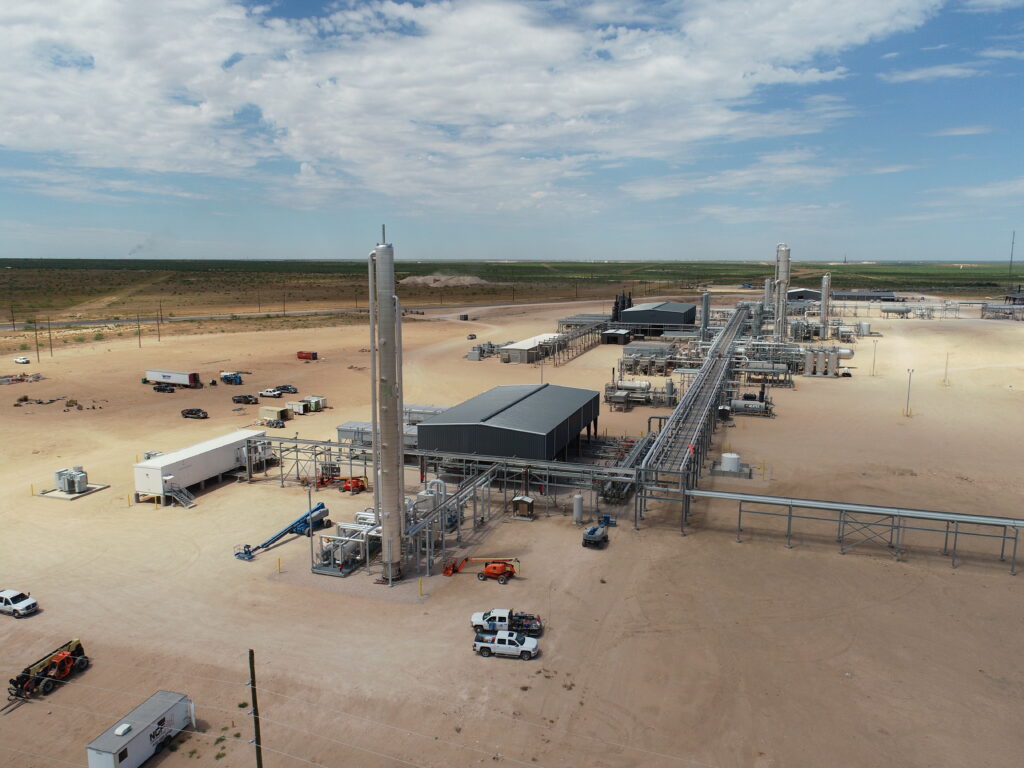
NiTech® Single Tower
- Robust design enabling processing of higher inlet N2 streams
- Ideal for landfill applications
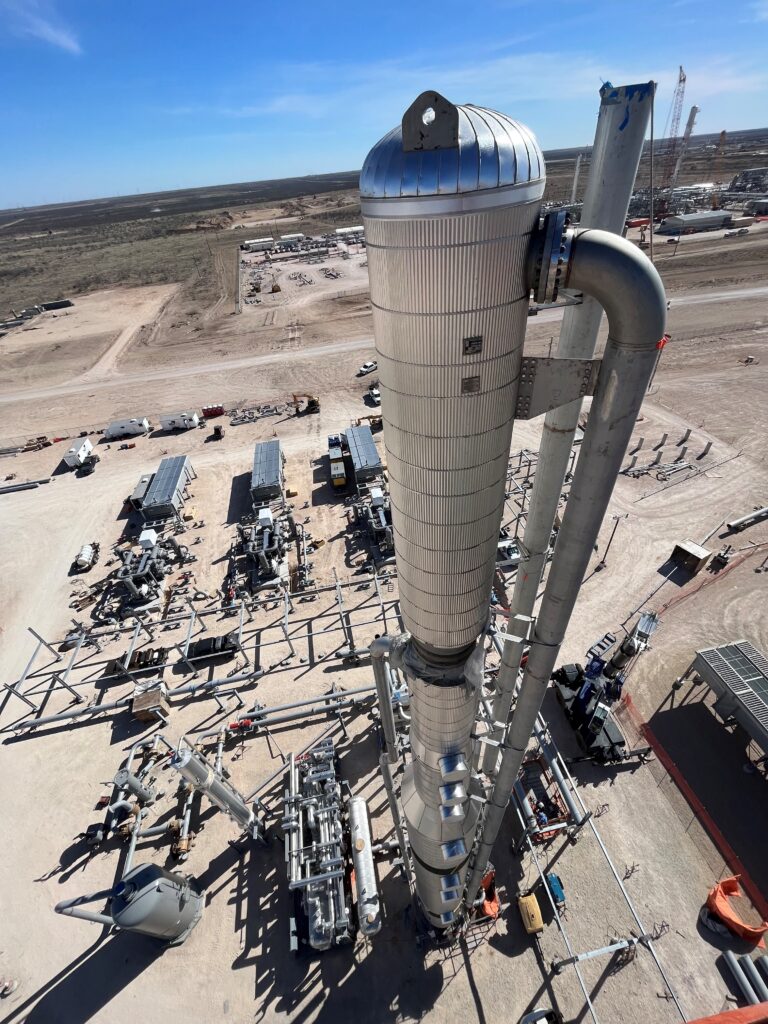
NiTech® Dual Tower
- Utilizes BCCK’s single tower design with the addition of an LP processing section
- Targeted for lower N2 inlet gas streams.
- Yields 10-15% lower required HP than the most efficient single tower processes
- Higher CO2 tolerance than a single tower NRU
- Proven design that has become the industry standard for post NGL facility N2 removal
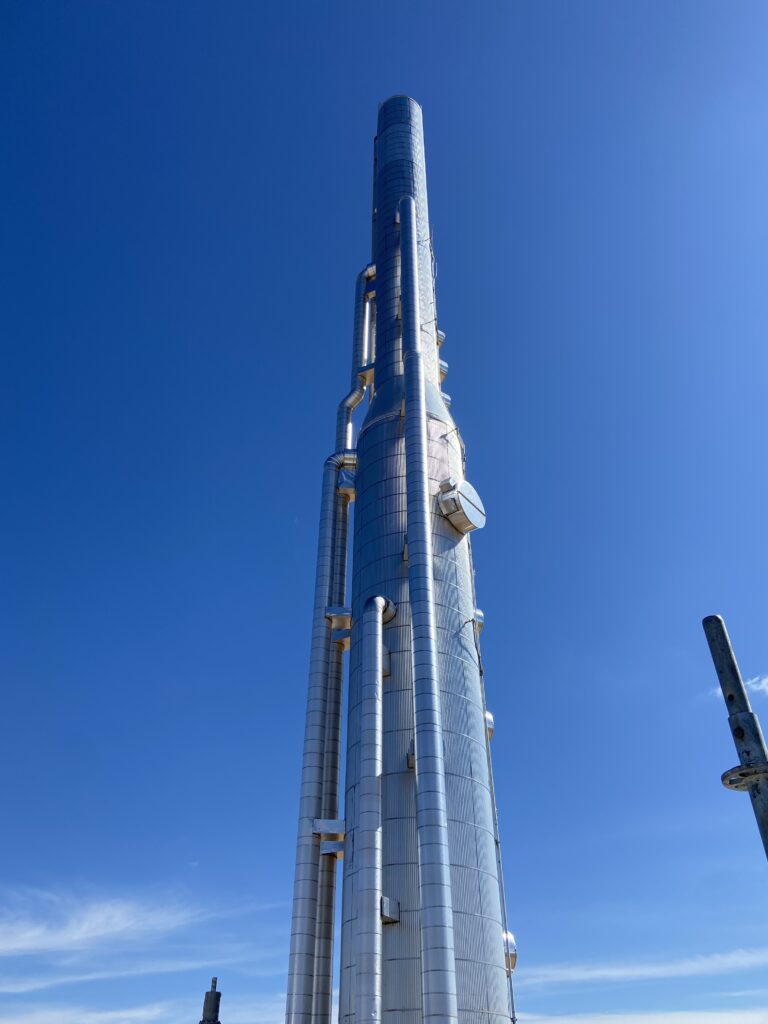
NiTech® ULM (Ultra Low Methane Enhancement)
- Patent-pending design utilizes BCCK’s proven NiTech NRU with a small compressed reflux system
- Engineered to provide an ultra-clean vent stream with reduced methane content as low as 10 ppmv, resulting in minimal methane losses to the environment
- Includes minimal equipment in addition to the NiTech NRU
- Available for new facilities or retrofitted to existing NiTech units.
>>LEARN MORE: Understanding NiTech® NRU Styles and Applications
No Real Unknowns (NRU) with BCCK
The separation of nitrogen and methane can be extremely difficult compared to the typical cryogenic NRU distillation of natural gas due to small differences in volatility, low surface tension and close boiling points. Combine this with full heat integration, deep cryogenic temperatures and 2-phase flow all throughout the process, and you have a minefield of issues that have caused even ‘experienced engineers’ to fail.
BCCK has proven that we have the experience and know-how to convert these challenging process designs into operational nitrogen rejection units that meet and typically exceed our client’s performance requirements.
This empirical aspect that goes into BCCK’s designs is invaluable and can only come from the lessons learned of an NRU’s actual startup and operation, not from running process simulations. The BCCK team has greater process engineering and operational pedigree than anyone to ensure a successful NRU project. Failure is not, and has never been, an option!
Nitrogen Rejection (NRU) Highlights
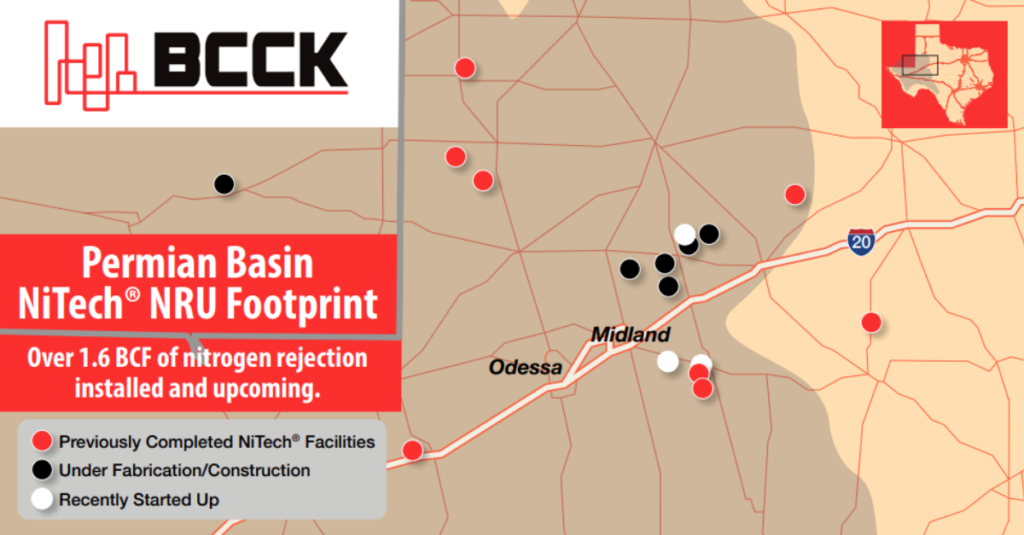
FEATURED ARTICLE
Growing LNG Exports Help Drive Improvements to Nitrogen Rejection Units
BCCK Senior Process Engineer Brennan Heiser explores actionable strategies for managing emissions while achieving broader operational goals.
NiTech® Benefits
- Low capital cost – only minimal equipment
- Flexible design allows a wide range of inlet conditions
- Low power consumption
- Simple, non-complex process design requiring minimal operator attention
- Small footprint due to minimal equipment
- Compression horsepower much lower than non-cryogenic NRU options
- Nitrogen contents from 3 percent to 90 percent reduced to as low as 1 percent
- High efficiency – hydrocarbon recovery typically in excess of 99 percent
- Environmentally friendly – emits no non-methane VOCs
- Quick restart
- Cold restart from short shutdowns, online and on-spec just restart associated compression
- Integrated NGL extraction with high NGL extraction efficiencies (up to 93 percent ethane recovery possible)
- Integrated helium extraction with high helium recovery
- Applicable to streams of 5 MMSCFD to more than 500 MMSCFD
Nitrogen Rejection Unit (NRU) Experts – BCCK
Separating nitrogen from methane is one of the most challenging processes in natural gas treatment due to low volatility differences, close boiling points, and deep cryogenic temperatures. Unlike typical cryogenic distillation, NRU design requires advanced solutions to handle 2-phase flow and full heat integration. At BCCK, we specialize in designing and operating highly efficient nitrogen rejection units that exceed client performance expectations.
Our expertise in NRU design comes from real-world startup and operational experience, not just process simulations. With a proven track record and unmatched engineering pedigree, the BCCK team ensures every NRU project is a success. Trust the industry leaders in nitrogen rejection technology for reliable performance. Failure is not an option with BCCK.
Why Choose BCCK for Nitrogen Rejection Units (NRU)?
- Expert NRU engineering with decades of operational experience.
- Proven designs that maximize efficiency and performance.
- Tailored solutions for even the most complex natural gas separation challenges.
EARLY NITROGEN REJECTION PROJECT
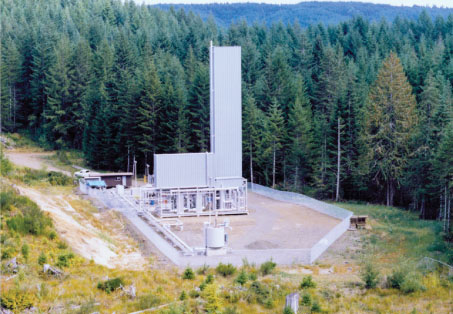
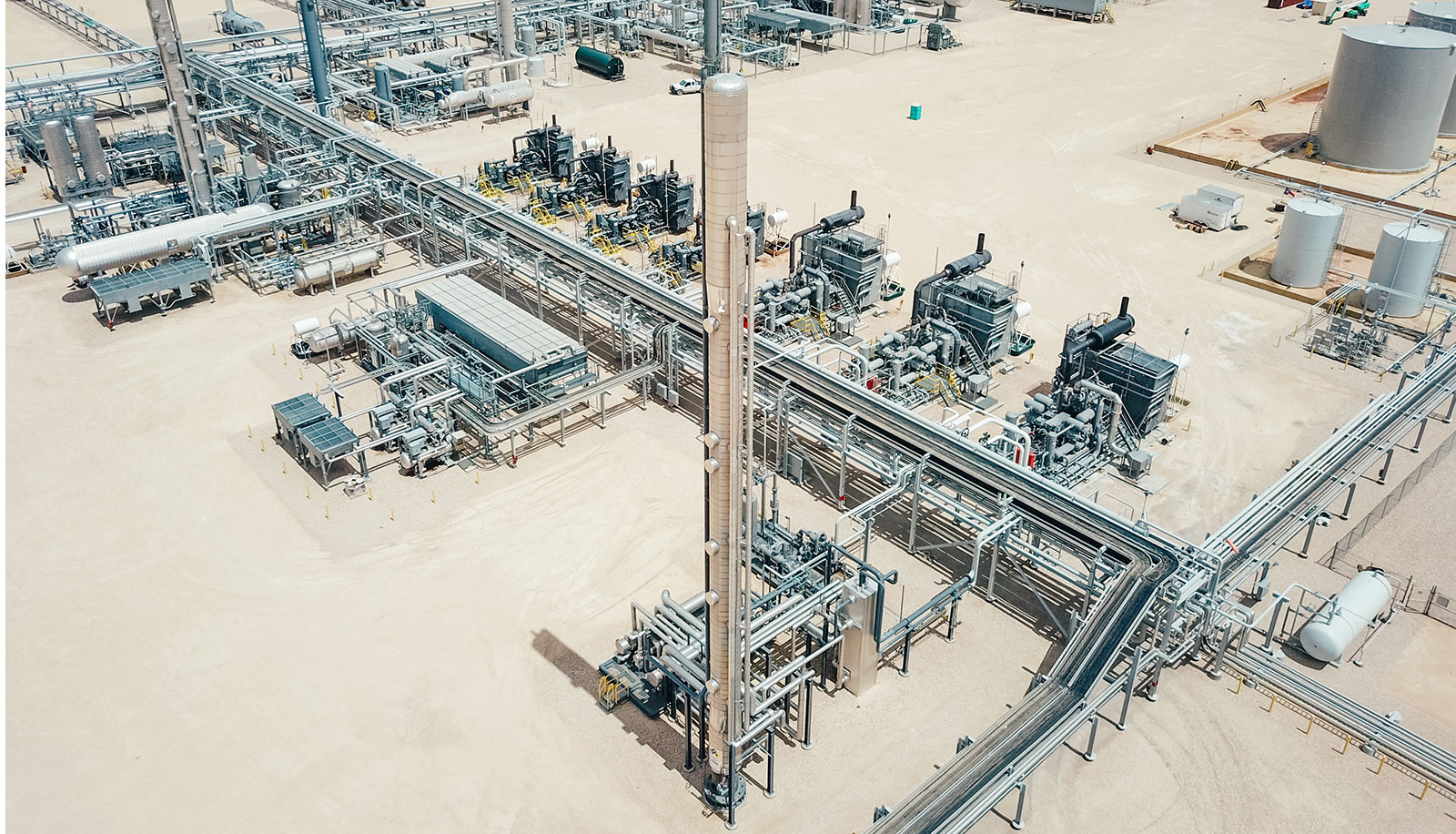
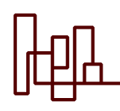
BCCK HISTORY
BCCK’s first NiTech® Nitrogen Rejection Unit installation was built in 1994 in Mist, Oregon.
BCCK began with traditional natural gas processing and treating systems, oilfield production installations and petrochemical facilities in the Southwest United States. Over time, as engineering projects became more complex and more varied, our client base expanded geographically and our technology expanded to profitably treat and process non-traditional gas, as well.
In the late 1980s, Clark Butts, BCCK’s founder, recognized the demand for an efficient, economical nitrogen rejection process for natural gas streams with volumes less than 30 MMSCFD. Butts developed and patented the NiTech® process, which BCCK has implemented throughout the United States. Since its introduction to the gas industry, the NiTech® nitrogen rejection process also has been used to process coal mine methane, thus reducing the emission of greenhouse gases.
Today, BCCK serves the natural gas industry with high quality and unique gas processing solutions.
FEATURED NRU IMAGES
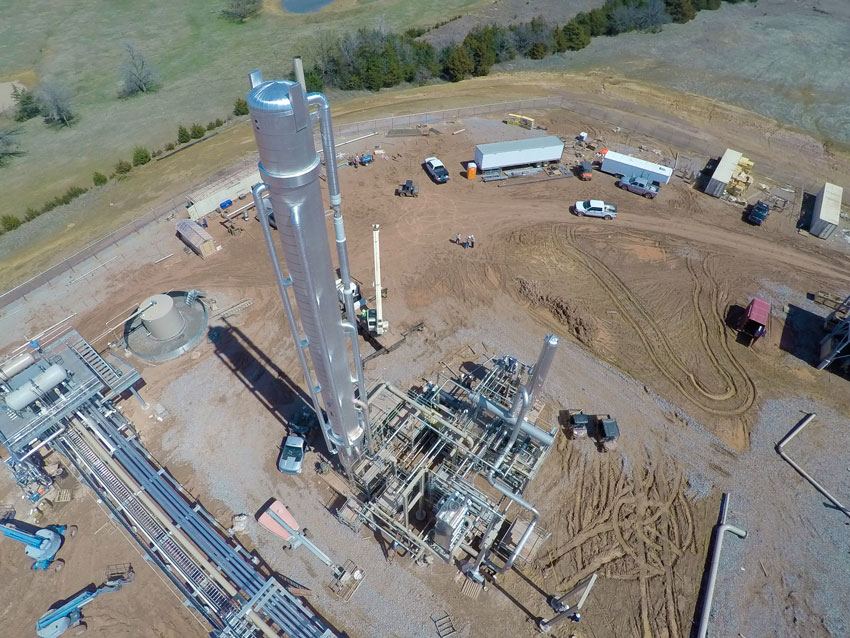
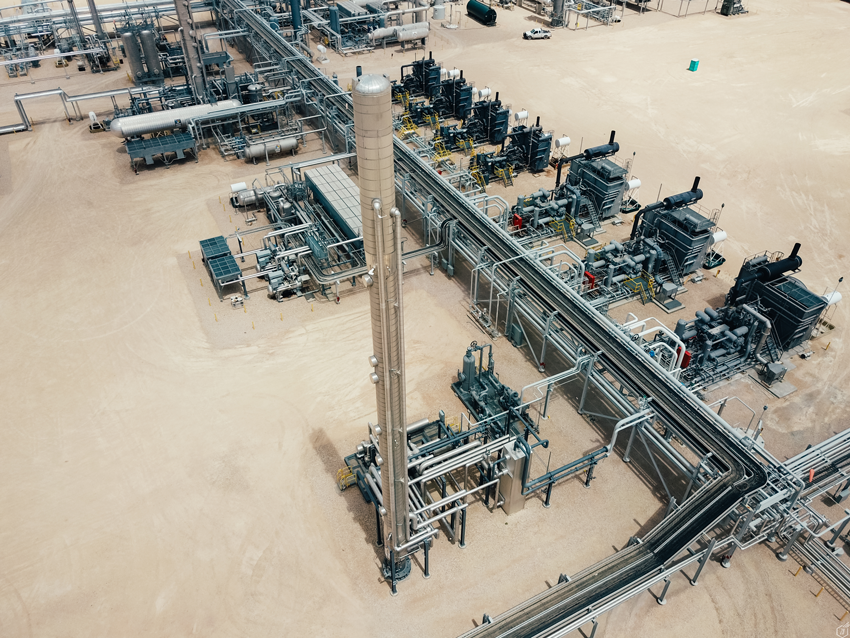
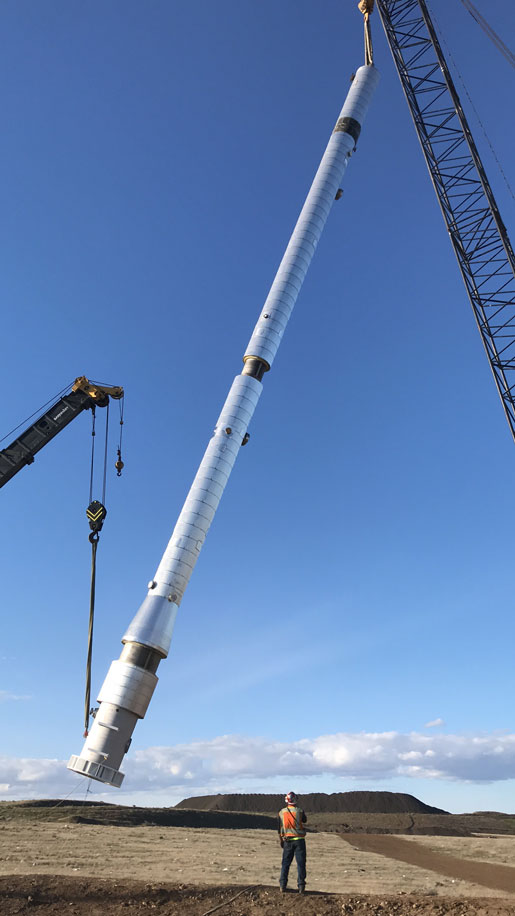
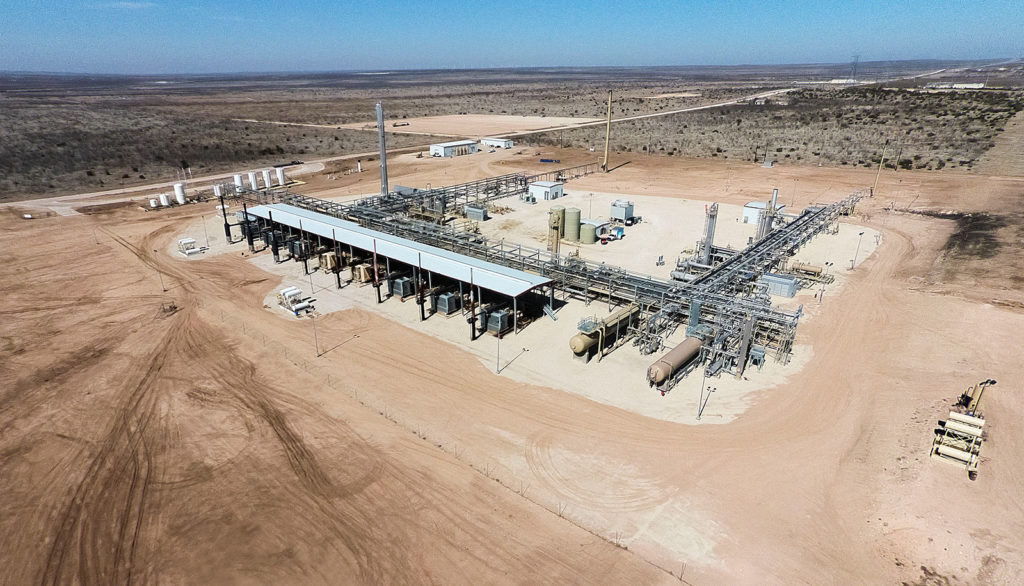

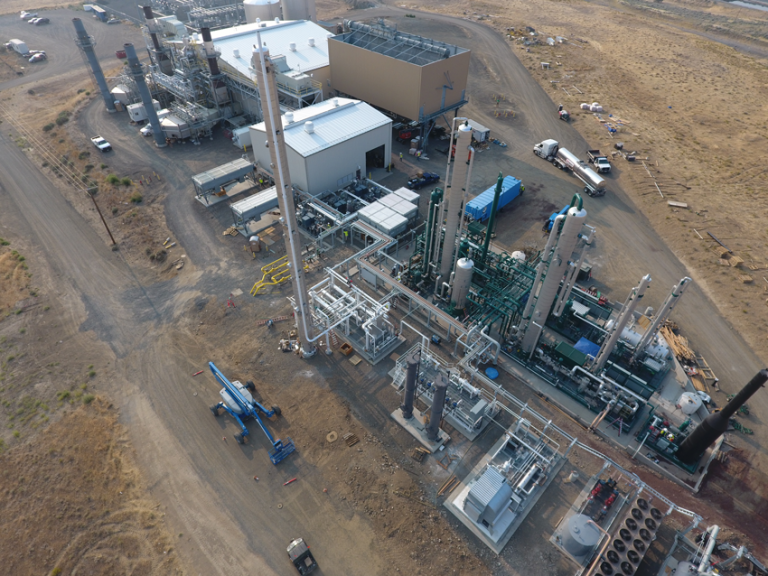